Zeolite rotor + high-temperature oxidizing furnace (TO):
The VOCs exhaust gas emitted by the enterprise in the production process enters the zeolite rotor for adsorption, and the clean gas after adsorption is discharged through the chimney to meet the standard, and a filter is set at the inlet of the exhaust gas from the zeolite rotor to remove particles in the exhaust gas. Cooling gas through the zeolite rotor cooling zone pre-heating and then through the heat exchanger to the required temperature of desorption, into the desorption zone of the zeolite rotor, to remove the organic components adsorbed in the molecular sieve, desorption of the exhaust gas from the desorption fan pressurized into the TO furnace for direct combustion. Greenstar environmental protection zeolite rotor + high temperature oxidation furnace TO direct-fired TO furnace, regenerative thermal oxidation decomposer, also known as direct-fired thermal oxidizer. The basic principle of the main body consists of a combustion chamber and three ceramic filled beds. When the exhaust gas passes through the ceramic beds, it is heated above 800℃ and oxidization reaction occurs, producing carbon dioxide and water. The heat released during decomposition is also recovered to achieve the dual purpose of environmental protection and energy saving.
Zeolite rotor + high temperature oxidizer (TO) process flow:
VOCs gas collection → dry/wet filtration → zeolite rotor adsorption and concentration → high-temperature oxidizing TO → blower + chimney (standard discharge)
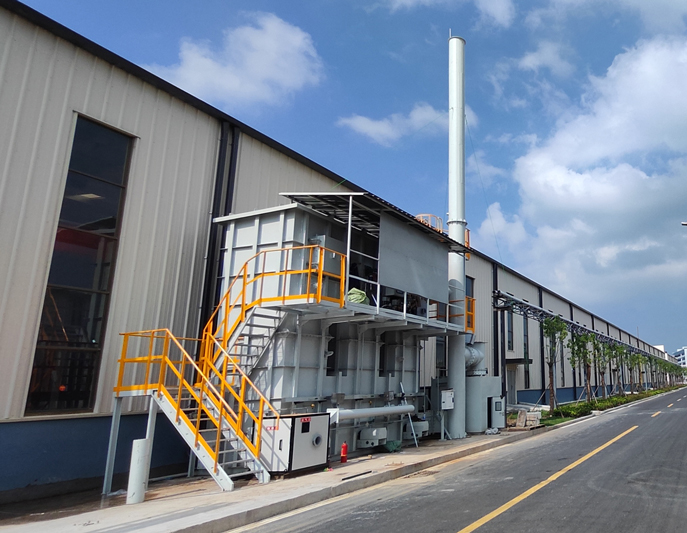
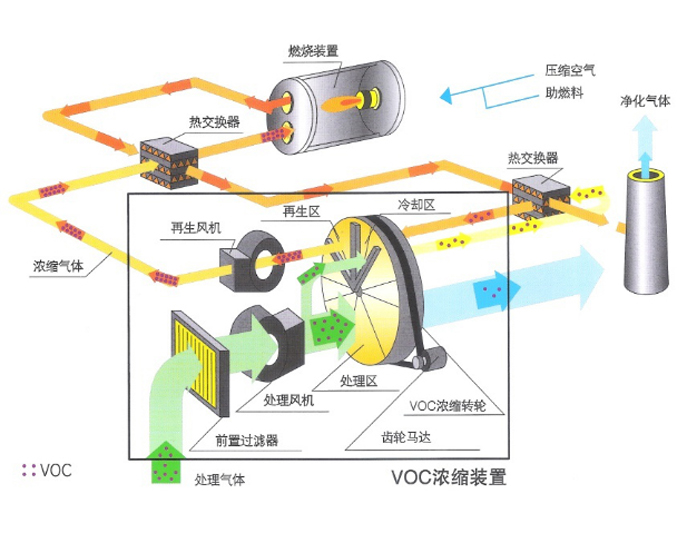